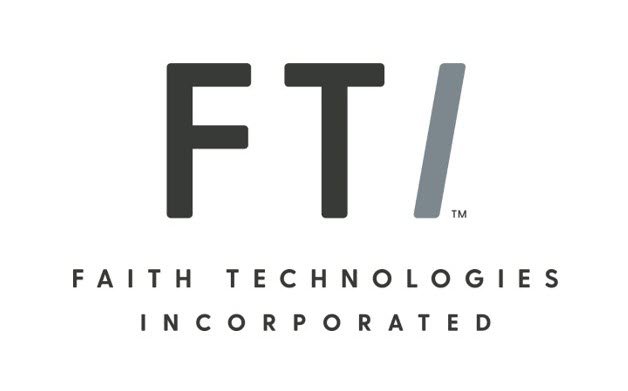
Faith Technologies Inc. is a national leader in engineering, construction, manufacturing and clean energy.
- Antiquated facility
- Remote location
- Inefficient business model
- Limited data access & reporting capabilities
- Facility & systems upgrades
- FactoryTalk® View SE
- FactoryTalk® ViewPoint
- FactoryTalk® Historian
- PowerFlex® 750-series Drives
- PlantPAx® Distributed Control System
- Increase in daily gas output
- Reduced monthly downtime
- Real-time data collection
- Improved reporting
- Remote access
Wade Leipold is executive vice president of Faith Technologies Incorporated (FTI), a national leader in engineering, construction, manufacturing and clean energy. The firm is a gold-level member of the Rockwell Automation PartnerNetwork™. Leipold’s responsibilities include FTI’s systems integration and automation solutions.
Challenge
Antiquated Facility & Inefficient Business Model
One of FTI’s clients operates a biodigester facility in Middleton, Wisconsin that converts cow manure into renewable natural gas. At the time, the facility was burning the natural gas to create electricity.
“That business model wasn’t working very well, and they wanted to change the process to refine the natural gas and inject it right into the natural gas pipeline,” Leipold said. “The facility was also antiquated, so they wanted to do some updates. And because it was located 100 miles away, they wanted the ability to access, monitor and troubleshoot remotely as needed.”
Additionally, generating and reporting historical data was a problem.
“Facilities like this one are measured by a CI (carbon intensity) score that indicates the amount of greenhouse gases emitted to produce an amount of energy. The lower the score, the more valuable that gas is,” Leipold explained. “They needed a control system that could capture that data, report it and provide a true value for their gas.”
Solution
Facility and System Upgrades
As part the client’s facility and systems upgrade, FTI implemented several FactoryTalk® software products.
“We used FactoryTalk® View SE so they could perform the monitoring, FactoryTalk® ViewPoint to enable remote access, and then FactoryTalk® Historian for collecting data,” Leipold said. “Additionally, we updated the controls and some of the drives. Specifically, we did PowerFlex® 750 drive upgrades throughout the facility, and then implemented the PlantPAx® distributed control system for overall control and data capture.”
The client already had Rockwell Automation equipment in place at this facility, which Leipold said made it easy to proceed with the upgrades. Leipold credits the client’s initiative to engage FTI early in the planning process as critical to the project’s success.
“We were able to understand their challenges, come up with a plan to mitigate those challenges, and put a specific solution in place,” Leipold said. “Then we continued to follow up to make sure they were getting what they needed from the system.”
Result
Increased Output & Reduced Downtime
Now with the ability to collect real-time data and remotely access the facility controls, FTI’s client can more easily monitor, maintain and resolve issues. They’re able to generate the necessary reports. And the local and cloud-based storage provides system resiliency.
“It was great partnering with Rockwell Automation to develop and implement the solution to support this client,” Leipold said. “They have seen a lot of improvements. Overall, their downtime losses are going down month over month, and they're also producing more gas.”
Liepold estimates the biodigester gained more than 139 therms of gas per day over the past year. One therm is equal to 100,000 BTUs.
Visit our Renewable Energy Page to learn more about how we’re helping companies accelerate the energy transition.
Published April 24, 2024